El oxicombustible crea una reacción química entre el oxígeno y el acero que está tan caliente (alrededor de 1800 °F) que el metal se ablanda y luego se derrite.
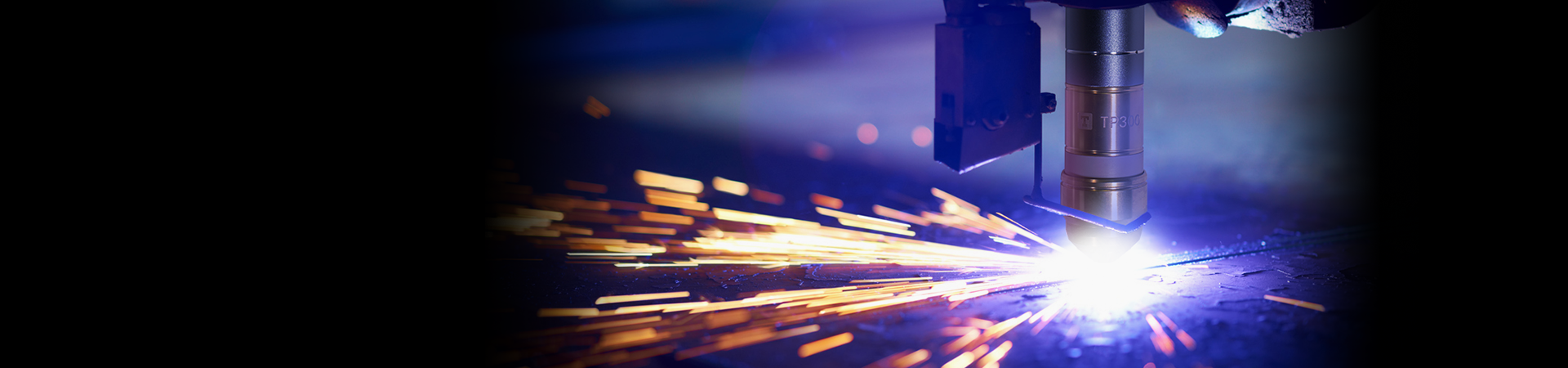
- CONOCIMIENTO BÁSICO
- CARACTERÍSTICA
- COMPARACIÓN
- CALIDAD DE CORTE
- PRODUCTIVIDAD
- COSTO OPERACIONAL
- Contacto
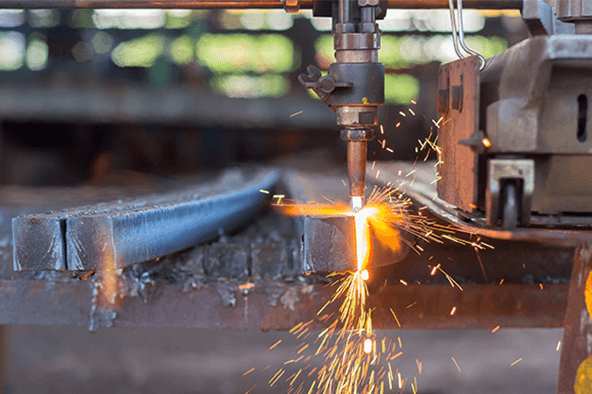
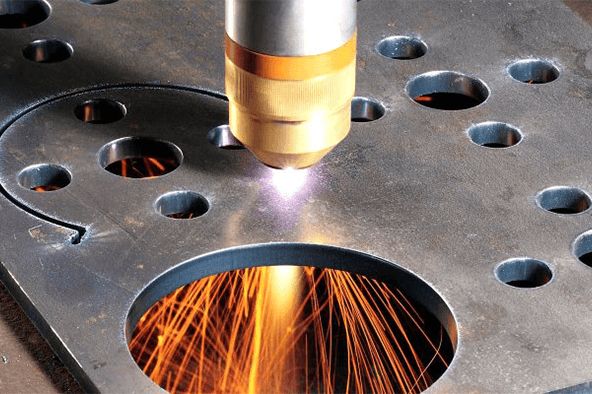
El plasma utiliza un gas ionizado a alta temperatura para producir un arco muy caliente y de alta densidad de energía que puede cortar cualquier material conductor.
El oxicombustible crea una reacción química entre el oxígeno y el acero que está tan caliente (alrededor de 1800 °F) que el metal se ablanda y luego se derrite.
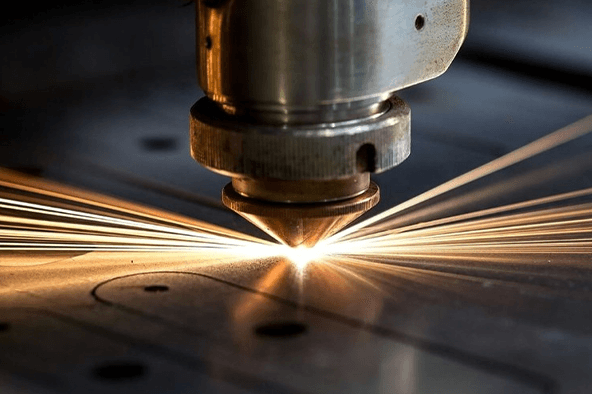
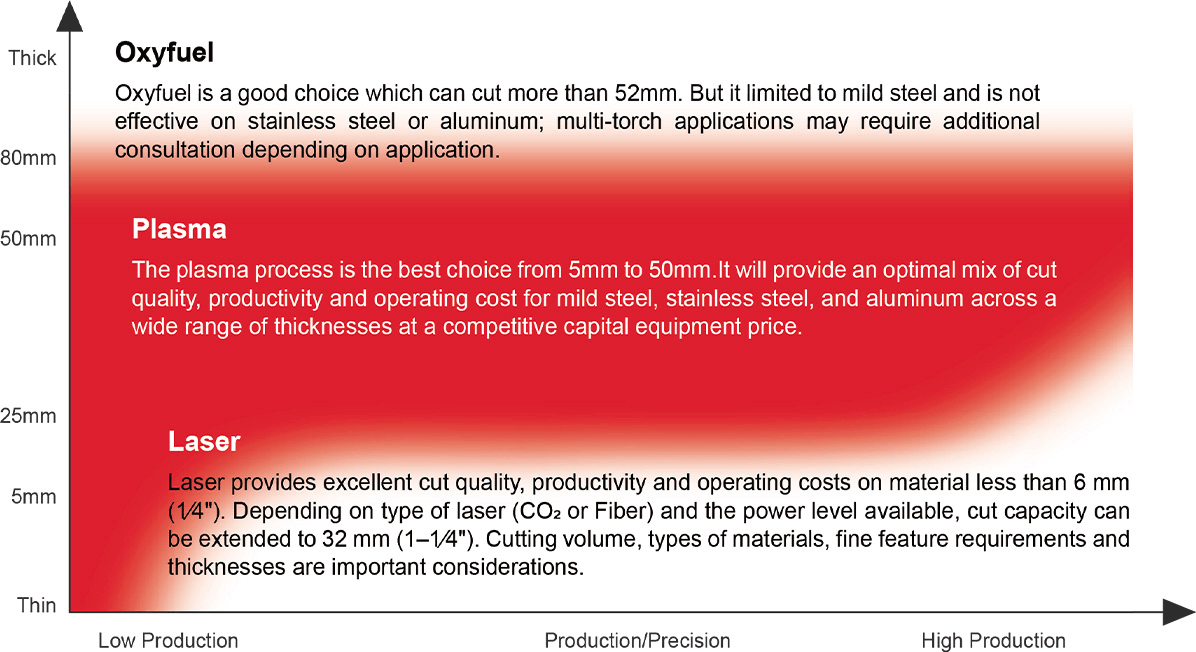
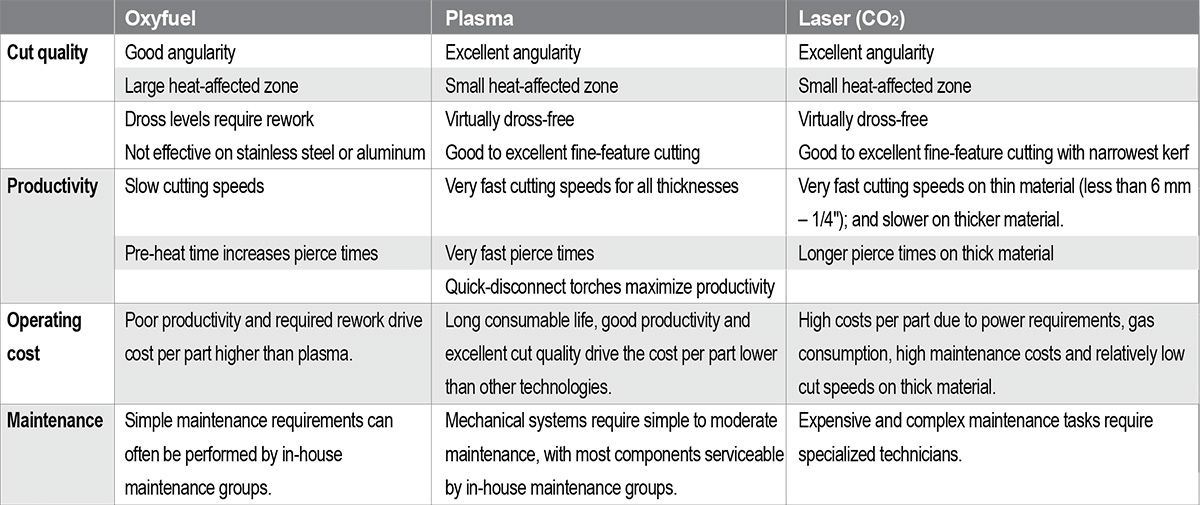
Diferentes aplicaciones de corte requieren diferentes niveles de calidad de corte. Esto puede ser importante porque el borde cortado será visible para el comprador de la pieza o producto terminado. En otros casos, la calidad del corte importa por su impacto en los procesos posteriores, como la soldadura o la pintura; los cortes listos para soldar reducirán la necesidad de preparación de la soldadura, lo que agilizará la producción y reducirá los costos de mano de obra. También hay momentos en los que la calidad del corte es de menor importancia y los operadores pueden optar por cambiar la calidad del corte por un mayor rendimiento.
La calidad del corte está determinada por una serie de factores que incluyen:
· El movimiento de la máquina de corte
· Si el nivel de potencia de la máquina se adapta bien al grosor del material que se está cortando
· Qué gases (o en el caso de chorro de agua, abrasivos) se están utilizando
· Si la configuración de la máquina y los consumibles de corte coinciden correctamente
Con algunos procesos, especialmente el corte con oxicorte, la habilidad del operador puede ser la variable más importante para determinar la calidad del corte. Otros procesos no dependen tanto de la habilidad del operador.
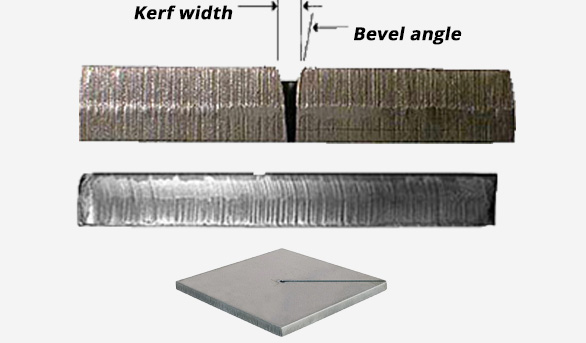
La calidad de un corte se evalúa de acuerdo con las siguientes propiedades:
· Angularidad: se considera mejor un corte con poco o ningún ángulo
· Corte o ancho: un ancho de corte más pequeño permite un detalle más fino de la pieza
· Tolerancia: tolerancias más estrictas significan un corte más preciso y repetible
· Tamaño de la zona afectada por el calor: una zona más pequeña protege mejor la integridad del metal y afecta la viabilidad de otros procesos, como la soldadura y el roscado.
· Escoria: generalmente menos es mejor (la escoria es metal que se derrite durante el proceso de corte y permanece adherido a los bordes del corte)
· Calidad de los bordes − suavidad del acabado
· Rendimiento del control de altura de la antorcha (THC)
A menudo, la productividad se equipara incorrectamente solo con la velocidad de corte. Si bien es importante, también hay otros factores a considerar. Por ejemplo:
· Cantidad de tiempo de programación requerido
· Tiempo requerido para la configuración del trabajo en la máquina de corte
· Tiempo necesario para preparar (o precalentar) el sistema para el corte
· Número de cabezales de corte que puede aceptar la máquina
· Eficiencia del software de anidamiento y su capacidad para maximizar el tiempo de corte y reducir el movimiento innecesario del cabezal de corte
· Capacidad para descargar piezas de forma segura mientras el sistema está cortando
· Capacidad para realizar múltiples procesos en una sola máquina, por ejemplo, cortar contornos, cortar ranuras y orificios interiores y biselar
· La integración de sistemas para realizar tareas paralelas, como preflujo durante la poligonal o IHS, puede mejorar el tiempo del proceso
· Tiempo necesario para operaciones secundarias como el rectificado, que puede reducirse o eliminarse mejorando la calidad de las piezas que salen de la máquina de corte
Muchos factores pueden afectar el costo total de operación de un sistema de corte: consumibles, energía, gas, mantenimiento, etc.
Costo de producción
El costo de la mano de obra también contribuye de manera importante a los costos operativos en la mayor parte del mundo; El aumento de las tasas de mano de obra y la falta de mano de obra calificada continúan impulsando la demanda de soluciones de corte automatizado. Para mejorar aún más los costos operativos, considere una solución totalmente automatizada que pueda reducir o eliminar:
· la necesidad de programación y configuración en el CNC
· operaciones secundarias como esmerilado para preparación de soldadura
· la necesidad de más de una máquina para realizar múltiples operaciones de proceso, como corte, marcado y biselado
Utilización de materiales
La utilización de materiales es otro contribuyente importante a los costos operativos. Si bien en muchos casos es posible recuperar parte del costo vendiendo material sin usar o de desecho, es mucho más beneficioso aumentar la utilización de ese material para que haya menos desperdicio en primer lugar. Una variedad de factores contribuyen a la utilización del material; en particular, el software CAD que determina el nido de piezas y dirige el movimiento de corte.
Al calcular el costo operativo, es importante evitar calcular solo el costo por hora y, en su lugar, centrarse en el costo por pieza o el costo por pie. ¿Por qué? Un sistema cuyo funcionamiento cuesta ~$17,96 EUR ($20) por hora pero que solo produce dos piezas por hora no es tan eficiente como uno que cuesta ~$17,96 EUR ($20) por hora pero produce 100 piezas.
Costo por pieza = Costo operativo por hora / número de piezas producidas
Costo por pie = Costo operativo por hora / número de pies cortados
Coste total
Una evaluación aún más profunda del costo operativo requiere comprender el costo total para producir una pieza completa, incluidos los procesos posteriores para preparar la pieza para soldar o pintar, o simplemente terminar la pieza con fines estéticos. Cuando los procesos posteriores, y el tiempo de máquina y los costos de mano de obra que requieren, pueden reducirse mediante mejoras en el proceso de corte, el costo total por pieza completa puede reducirse.
Un área que a menudo se pasa por alto en un sistema de corte es el rendimiento del control de altura de la antorcha (THC). Un control de altura de alto rendimiento tiene la capacidad de configurar procesos automatizados a través del CNC o el programa de piezas para:
· reducir o eliminar errores comunes de configuración
· compensar el desgaste de los electrodos para maximizar la vida útil de los consumibles
· mantener la altura adecuada para una óptima angularidad de corte
· detectar colisiones de la antorcha protegiendo la antorcha de daños